3D modeling is a great way to build things because it lets you see things in a very realistic way, take accurate measures, and use efficient workflow tools that speed up product development and lower costs through virtual testing. Many businesses now turn to professional 3D modeling services to take full advantage of these benefits.
However, these great benefits come with big problems, such as having to buy a lot of hardware and software, getting steep learning curves, and having technical problems like render times.
So, the technology’s amazing accuracy and image benefits should be carefully weighed against its cost, technical difficulties, and usefulness issues to determine if it’s right for your needs.
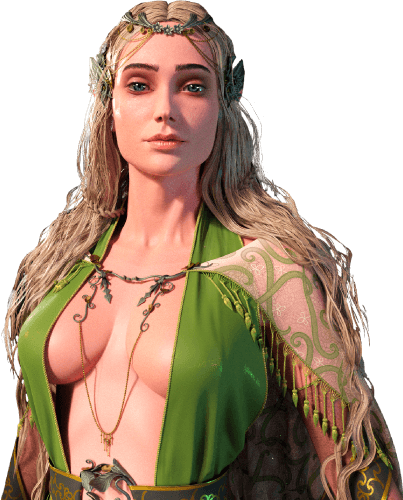
Need 3D Animation Services?
Visit our 3D Animation Service page to see how we can help bring your ideas to life!
Top 8 Advantages of 3D Modeling
3D modeling makes accurate digital models that speed up design, make it easier for people to work together, and let you try designs virtually before they are made in real life.
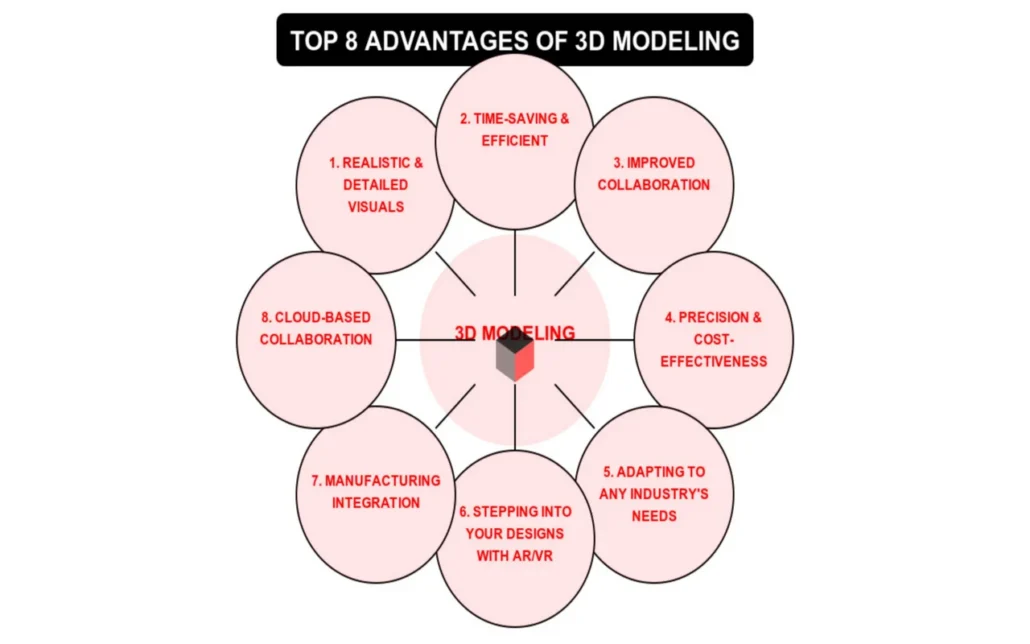
1- Realistic & Detailed Visuals
What’s so great about 3D modeling? It makes images look incredibly real thanks to its high-fidelity backgrounds, perfect lighting, and striking shadows—qualities that also influence the overall 3D character model cost.
- Precise material properties: Reflectivity (0-1), transparency, and roughness values that perfectly match real-world physics
- Flexible lighting: Adjustable conditions showing designs in different environments, measured in lumens and Kelvins
- High-res texture mapping: Up to 8K resolution (7680×4320 pixels) without complex geometry
- Dynamic viewing: Instant camera angle changes with focal lengths from 14mm to 200mm
- True spatial accuracy: Sub-millimeter precision showing real scale and proportion
- Incredible detail visibility: Fine details as small as 0.01mm that 2D drawings might miss
- Extensive material testing: Hundreds of variations without physical samples, saving weeks
2- Time-Saving & Efficient
The 3D modeling process really speeds up the planning process because you can quickly change current models instead of starting from scratch each time. Plus, you can use the same images for multiple projects, which cuts down on unnecessary work and speeds up the time it takes to finish.
- Parametric modeling: Automatic measurement updates across the model, reducing changes from hours to seconds
- Design iterations: 4-6 hours vs traditional 3-5 days
- Component libraries: Thousands of ready-to-use common components
- Multiple views: Generate dozens of views/parts from a single 3D model with few clicks
- Automatic updates: Instant whole-model updates when any part changes
- Design variations: Test 5-10 different versions quickly vs the previous 1-2
- Last-minute changes: Easy modifications 24-48 hours before deadline without extensive rework
Read More: How Long Does it Take to Make a 3D Model?
3- Improved Collaboration
What about working together as a team? 3D modeling makes it much easier to do so because it lets everyone see what is being said to get past language hurdles and hard-to-understand scientific terms. Together, teams can share, look over, and change ideas. Why this is a good idea:
- Global teamwork: Teams across different countries and time zones can view and communicate with the same model simultaneously
- Client understanding: Complex concepts become accessible to clients without technical expertise
- Targeted feedback: Digital notes and measurements enable precise feedback on specific model areas
- Multi-department collaboration: Engineering, design, and marketing can work together using one reference
- Version tracking: Timestamped history allows tracking changes linked to individual team members
4- Precision & Cost-Effectiveness
More impressively, 3D modeling provides incredibly accurate measurements and connections between objects while also saving money by getting rid of the need for costly physical samples. Virtual testing finds mistakes in the design before making it, so you don’t have to make those painful and expensive changes later.
- Accuracy: Precise measurements within 0.001mm (1 micron) ensure proper part fitting
- Material efficiency: Exact material calculations reduce waste and overordering by 15-20%
- Online testing: Thousands of load estimates can be run directly on the model
- Tool optimization: Using validated models saves $5,000-$50,000 per tooling fix
- Budget accuracy: Detailed material and production data make cost projections accurate within 3-5% of final costs
Read More: How Much Does 3D Modeling Cost?
5- Adapting to Any Industry's Needs
We can all agree that 3D modeling techniques are very useful. It’s like that one tool that works ideally whether you’re making medical instruments or buildings. The technology itself doesn’t change, but it works great with anything you give it.
- Architecture: Business projects can include models with over 25,000 individual parts (windows, doors, lighting fixtures)
- Gaming: Between 10,000-30,000 models are used to create realistic characters players can connect with
- Healthcare: Medical teams create structural models from scan data accurate to within 0.5mm
- Manufacturing: Production teams develop tools with a precision of ±0.005mm (finer than a human hair)
6- Stepping Into Your Designs with AR/VR
AR/VR animation and 3D modeling services go together like peanut butter and jelly. You can explore places and communicate with things in real time when you use this combination—whether it’s for immersive AR/VR animation projects, creating detailed VR game art, or enhancing the overall experience of VR gaming.
- Architecture: You can explore your future home at its actual size before construction even begins
- Product Design: You can feel how comfortable that new chair is without building an actual prototype
- Training: You can experience dangerous situations safely without any real risk
- Medical Education: Medical students can perform practice surgeries on realistic 3D models
7- Manufacturing Integration
No longer do designers just “throw drawings over the wall” for production to follow. These days, 3D models go straight to tools that make things, connecting the imagined and the real.
- Direct Production: Instead of going through middlemen, you can send plans straight to CNC tools.
- Complex Geometries: 3D printing lets you make forms that you couldn’t make any other way.
- Automated Programming: You now can make tool routes instantly, which cuts days of programming time down to hours.
8- Cloud-Based Collaboration
When 3D modeling process is done in the cloud, teams that are spread out can work on the same models at the same time, with real-time changes and version control. No matter where they are, what time zone they’re in, or what tools they have, partners can view the same info.
- Global Teamwork: Teams in different offices or countries can work together on the same model at the same time
- Processing Power: Heavy rendering tasks run on powerful cloud servers instead of your own computer
- Version Control: Every change is saved with timestamps, and who made it
- Security Management: Custom access permissions for different team members or contractors
- Data Management: Share huge model files (2-5GB) without transfer problems
- Client Access: Clients can view models in regular web browsers without installing special software
- Scalable Resources: Computing power grows or shrinks based on what your project needs
- Mobile Flexibility: Review and approve models on tablets or smartphones while on the go
9 Disadvantages of 3D Modelling
3D modeling costs a lot, takes a long time to learn, causes problems with connectivity, and creates big files.
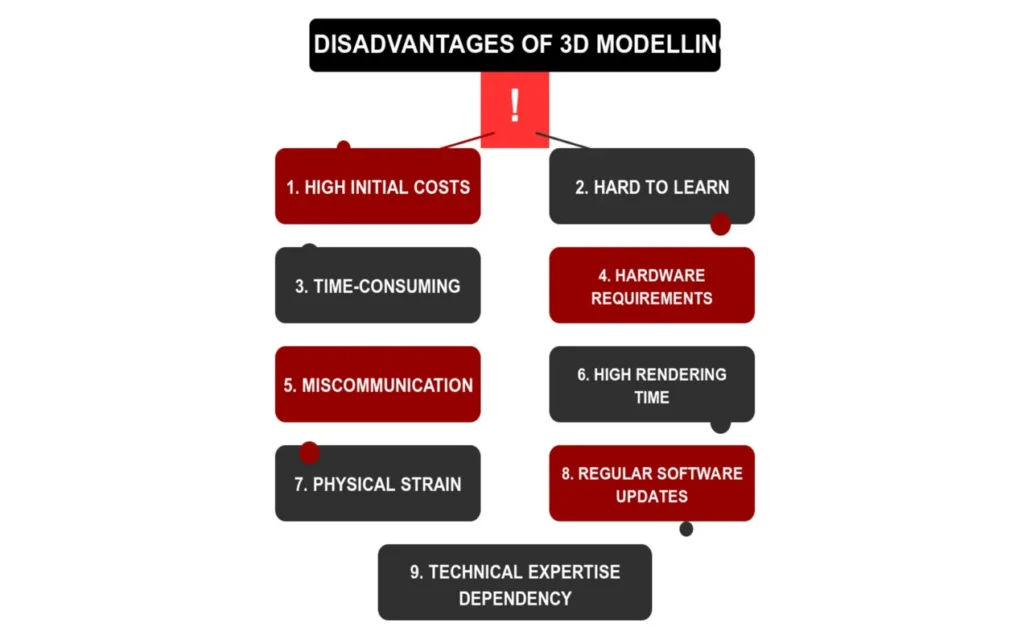
1- High Initial Costs
You will need to spend a lot of money to get started with 3D modeling. The initial cost can be very high, especially if you’re a small business, an independent creator, or a school that wants to add 3D skills to your operations.
- Professional 3D modeling software costs between $1,500 and $6,000 a year per spot.
- Need tools made for your industry? That will cost an extra $500 to $2,000 per cell.
- A good computer with a good graphics card costs between $2,000 and $5,000.
- Real drawing tools are often priced at more than $10,000.
- It charges between $500 and $3,000 per person to learn how to use the program.
- For cloud systems, monthly fees cost an extra $50 to $250 per person.
2- Hard to Learn
It’s not easy to just pick up and play 3D software. It takes a long time to figure out all of these programs’ thousands of tasks, tools, and functions. Newcomers often feel fully lost in all the technical details.
- It usually takes 3 to 6 months of regular practice to get the basics down.
- Getting really good at it? That’s more like studying hard for one to two years.
- Interfaces have 500 to 1,000 or more separate requests.
- It takes a lot of skill to be good at specialized methods like NURBS or subdivision modeling.
- Workflows that are tailored to each industry
- You have to remember 200 to 300 computer keys.
- It takes some time to get good at technical ideas like geometry and UV mapping.
3- Time-Consuming for Complex Projects
It takes a lot of time to make precise models and good images, especially for big tasks. So your schedules and planning for resources could be badly affected by this.
- Creating a realistic building model can take between 80 and 120 hours.
- It could take 40 to 60 hours to finish making complex figure models.
- Two to twenty-four hours could go into a single high-resolution accurate image.
- Want animation? Add 24 frames per second to that processing time.
- Changes and revisions add 20 to 50 percent more time to your original schedule.
- Modeling can take 200 hours or more for large settings like cityscapes.
- It takes an extra 15 to 30 hours per model to texture complicated models.
4- The Hardware Requirements
Honestly, 3D modeling uses a lot of resources. Just to get started, you need a computer with a great deal of power, a lot of memory, and special drawing skills. Sadly, these standards are not only expensive, they also make it hard for new people to join.
- Today, 3D software needs at least 6 to 8 core processors to run well.
- Prices for professional graphics cards with 8 to 16GB of VRAM will always be high- $800 to $2500
- You should have at least 32GB of RAM, and 64–128GB is recommended for anything even slightly complicated.
- Special control devices, such as 3D mice or tablets, will cost an extra $200 to $500.
- Quick storage? Basically, that’s 1 to 2 TB of SSD room to store your files and projects.
- You’ll need at least two 27- to 32-inch computers to see what you’re doing clearly.
5- Potential for Miscommunication
Those beautiful, photorealistic renders can seriously create expectation problems. What instantly looks “done” to a client might be miles from completion in reality.
- Clients often mistakenly think a good-looking render means the design is finished
- Pretty pictures can effectively hide serious technical problems or unresolved design issues
- Stakeholders get emotionally attached to specific visual elements shown in early concepts
- Teams focus excessively on making things look good instead of making them work well
- Non-technical people simply can’t tell the difference between a concept and a final design
- Creating presentation-quality visuals constantly eats the time you should spend on actual design
6- High Rendering Time
Believe me, it hurts to wait for rendering. High-quality 3D renders need a lot of computing power, which can slow down your whole production process. These output times don’t just take hours; they take days, which always throws off project schedules.
- It takes 4–8 hours to process a single 4K picture at full quality.
- Those beautiful building drawings with complicated lighting? You can expect at least 12 to 24 hours per frame.
- A 10-second clip at 24 frames per second needs 240 separate renders
- Product shots of materials that reflect light will keep your computer locked up for 6 to 10 hours per view.
- Glass and liquid simulations may easily take more than 30 hours for each frame
- It will cost around $10,000 to $100,000 to set up a real render farm.
- 2 to 5 dollars an hour per machine for cloud processing services will slowly drain your budget.
- Even checking your render settings over and over again takes 10 to 15 minutes each time.
7- Too Much Stress on the Body
Working with 3D modeling software for long periods of time can be very hard on your body and cause problems like eye tiredness, repetitive stress injuries, and bad posture.
- Focusing on small models can fatigue your eyes and lead to headaches and vision problems.
- Tendonitis and carpal tunnel syndrome can happen if you use a mouse or computer all the time.
- Sitting in the same place for 8 to 10 hours at a time can hurt your back and neck.
- Monitor light makes eyes tired after working nonstop for 2 to 3 hours.
8- Regular Updates for Software
There is never anything boring in the world of 3D software. Every update changes interfaces completely, adds new features, and regularly messes up established processes.
- Every year, major software versions drop, which totally changes the displays.
- Small changes sneak up on you 3 to 4 times a year, and each one needs time to get used to.
- It usually takes 5 to 10 hours of learning to fully master a new feature.
- It’s pretty much necessary to rebuild your whole process after some updates that drastically change core features.
- Every time there is an update, custom scripts and routines often stop working.
- Some updates require unexpected hardware changes to keep things running smoothly.
9- Depending on Technical Know-How
3D modeling calls for very specific technical skills that combine technical know-how, software expertise, and creative talent. This kind of knowledge is hard to find, expensive to keep, and makes a company very dependent on specialist talent.
- Most skilled 3D modelers need 3 to 5 years of training before they can do their job well.
- Technical experts in developed markets make between $60,000 and $120,000 a year.
- It is hard to find suitable people who are good at both technical and artistic skills.
- Unfortunately, when key expert staff leave or aren’t available, projects can stop totally.
- It takes between 6 and 12 months to train new team members before they can do their full job.
The Real Deal on 3D Modeling
Let’s get right to the point: 3D modeling does offer visualizations that change the game, pixel-perfect accuracy, and easy teamwork across many industries, but it also has a lot of problems.
When you sign up for those jaw-dropping digital prototypes with sub-millimeter accuracy and easy team workflows, you also agree to spend a lot of money on hardware, use software that is unbelievably complicated, and rely on a small group of technical experts.